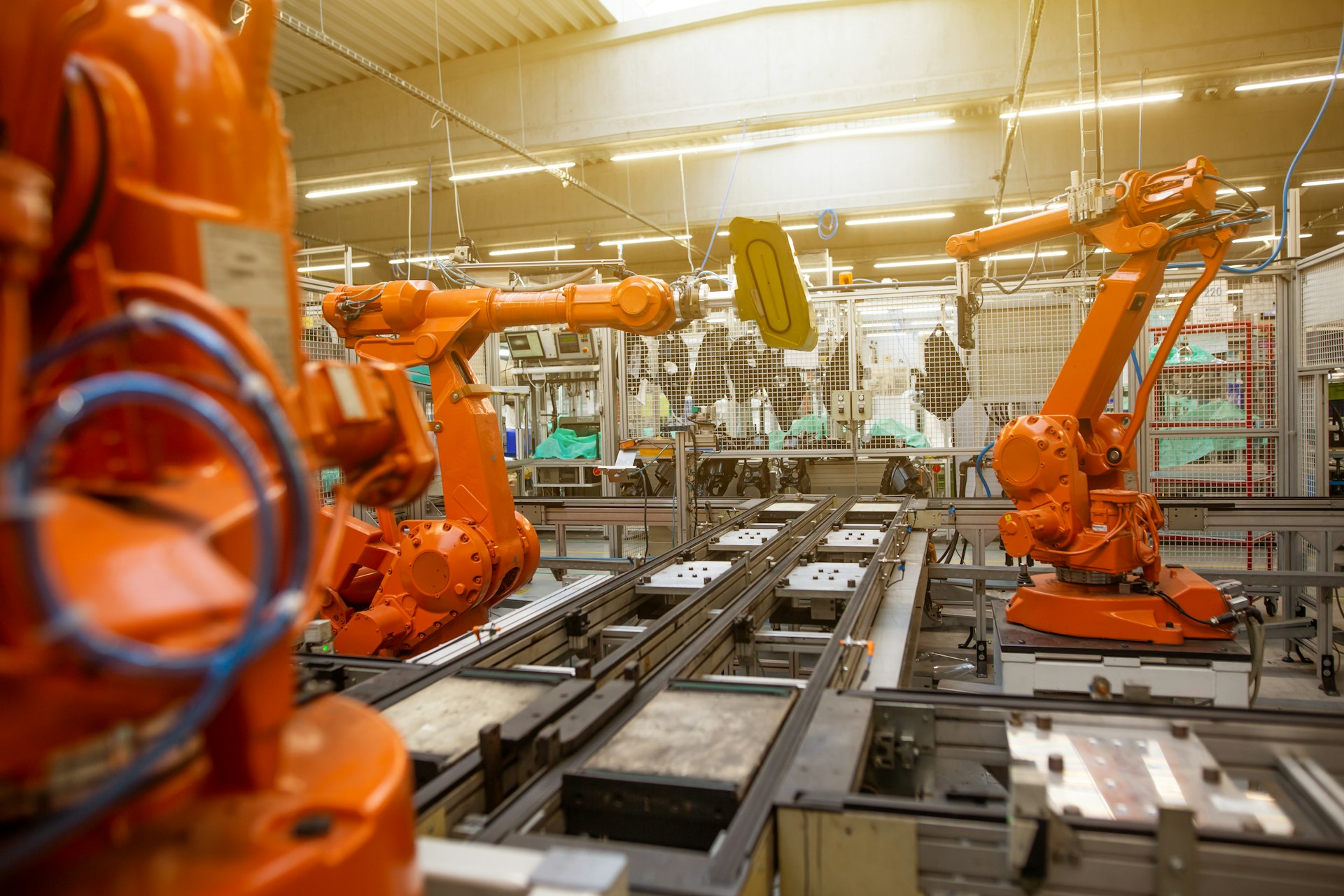
Case Study: Transforming Automotive Service Equipment with IoT Integration
Learn how Oakwood partnered with a global leader in automotive service equipment to transform their product offerings.
Summary
Overview
In today’s rapidly evolving automotive service industry, connectivity and data-driven insights have become essential for staying competitive. Our client, a St. Louis-based global leader in automotive service equipment, recognized the growing demand for smarter, more connected solutions. Despite their strong market position, they saw that their traditional equipment needed to evolve to meet the increasing expectations of their customers for real-time monitoring, predictive maintenance, and remote management.
To address these challenges, the client partnered with Oakwood to embark on a transformative journey to integrate Internet of Things (IoT) technology into their product offerings. The goal was not only to enhance the functionality and efficiency of their existing equipment but also to establish a scalable, future-ready platform that would support ongoing innovation. This initiative aimed to reduce downtime, improve operational efficiency, and deliver actionable insights that would set them apart in a highly competitive market.
Through our collaboration, we developed a comprehensive IoT solution that empowered the client to stay ahead of industry trends. This project not only met their immediate needs but also positioned them as an innovator in the automotive service industry, ensuring their continued leadership and ability to deliver cutting-edge products that meet the demands of modern customers.
Business Challenge
As a leading global manufacturer in the automotive service equipment industry, our client had built a reputation for producing high-quality, reliable products that technicians and service centers around the world depended on. However, with the rapid advancement of technology and the increasing prevalence of smart, connected devices, the industry was undergoing a significant shift. Customers were no longer satisfied with equipment that simply functioned; they wanted tools that could provide deeper insights, improve operational efficiency, and reduce downtime through predictive maintenance.
The client faced several key challenges in adapting to this new landscape. Firstly, their existing equipment, while robust and widely trusted, lacked the connectivity and data integration capabilities that modern service centers were beginning to demand. Without these features, the client risked falling behind competitors who were already adopting IoT and other advanced technologies. Moreover, their customers were increasingly seeking solutions that would allow them to monitor and manage their equipment in real-time, remotely diagnose issues, and receive data-driven insights to optimize their operations.
Additionally, the company faced internal pressures to improve service delivery and reduce the total cost of ownership for their products. Equipment downtime and unplanned maintenance not only disrupted their customers’ operations but also led to increased support costs and diminished customer satisfaction. To maintain their leadership position and meet these growing demands, the client needed to transform their product offerings by integrating IoT technology — an endeavor that required careful planning, technical expertise, and a clear vision for the future of their products.
Solution
Understanding the critical importance of connectivity and data in modern automotive service environments, Oakwood partnered with the client to develop a comprehensive Internet of Things (IoT) strategy tailored to their specific needs.
The solution involved embedding IoT sensors and devices across the client’s diverse range of automotive service equipment. These sensors were strategically placed to monitor key performance indicators (KPIs) such as equipment usage, temperature, pressure, and operational status. The collected data was then transmitted in real-time to a centralized cloud-based platform, where it could be analyzed and acted upon.
A customized IoT platform was developed to provide a unified interface for monitoring and managing the connected equipment. This platform included advanced analytics capabilities, enabling predictive maintenance by identifying potential issues before they led to equipment failure. Additionally, remote diagnostics were integrated, allowing the client’s support teams to troubleshoot and resolve issues from a distance, significantly reducing the need for on-site visits. The solution was designed with scalability in mind, ensuring that as the client expanded their product offerings, new equipment could be easily added to the IoT ecosystem. The system also incorporated robust security measures to protect sensitive data and ensure compliance with industry standards.
Conclusion
The implementation of our IoT solution led to transformative results for the client. Real-time monitoring capabilities significantly reduced equipment downtime by enabling proactive issue identification and response. This improvement in reliability directly enhanced customer satisfaction and loyalty.
Predictive maintenance minimized unexpected breakdowns and optimized the maintenance schedule, reducing unnecessary service interventions and associated costs. The data-driven insights from the IoT platform provided a deeper understanding of equipment usage, allowing the client to refine product designs and introduce features that better met customer needs.
Furthermore, remote diagnostics streamlined support operations, cutting down on response times and reducing the need for on-site technician visits. This not only improved operational efficiency but also strengthened the client’s reputation as an innovator in the automotive service industry, ensuring their continued leadership and success.
If you have any questions about your next technology initiative, please leave a note below for our Team.