The Future of Manufacturing
Creating agile manufacturing with Microsoft Technologies
There has never been a more exciting time to be a manufacturer. Manufacturers have a huge impact on our future. They will help build smart cities, autonomous vehicles, add intelligence to existing products from toasters to automobiles, help save energy and water, and fuel and feed the world through precision agriculture.
Over the next 5 weeks, we’re going to examine how Microsoft technologies are helping to shape the future of efficient manufacturers around the globe. From connecting employees, processes and machines to leveraging large data to ensure a more optimized supply chain – we’re going to take a look at how Microsoft technologies, along with expert partners like Oakwood, can help manufacturers thrive in the years and decades to come.
Overview
What we’ve been hearing from manufacturers like you that we’ve been engaged with in their digital transformation journey is that to get out of the commoditization trap and differentiate your products, manufacturers need to focus on their customers business outcomes, and to do that across their B2B and B2C customers the journey most manufacturers are embarking on is from production, to product-as-a-service.
This notion around transformation from production to product-as-a-service changes manufacturers whole mindset, and their business from end-to-end.
- They need more agile factories and responsive – and sustainable – supply chains
- They still need to focus on responsible and compliant manufacturing practices
- But now in addition, customers expect end-to-end security of their connected products-as-a-service
- And you need to address this transformation with a growing skills gap!
Manufacturers are coming to Oakwood because, in many cases, Microsoft’s technology already powers their manufacturing today, and they recognize IT convergence with OT (operational technology) can help address many of the above challenges.
Competitive edge is no longer based on product offerings alone. Now, manufacturing is about the best and most profitable business models and enhancing the customer experience.
The decreasing cost of IoT sensors, the increase in mobile devices, the scale of cloud-based platforms, and advances in traditional analytics as well as machine learning and artificial intelligence have created a tempest that is engulfing, changing, and opening almost every industry.
In manufacturing it’s no different. Customers are more knowledgeable, want more responsive experiences in purchasing and using products, and have more choices than ever before.
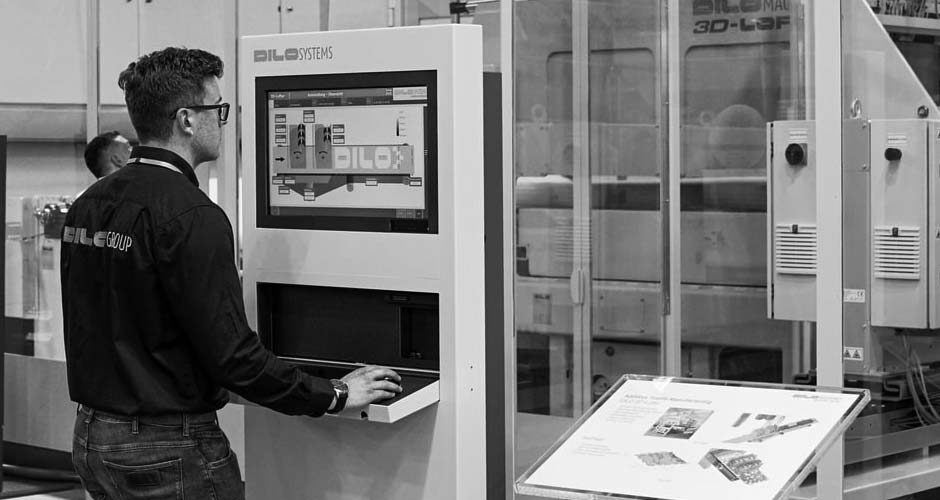
71%
71% of B2B companies lose customers due to a lack of deep engagement
80%
80% of manufacturers expect that improved factory connectivity will help them to increase output
83%
83% of manufacturers see a profit boost from selling services in addition to products
Top of mind for today’s manufacturer
Today’s manufacturer has responded to these trends by engaging in a complete transformation of how customers can experience their products. In traditional manufacturing, the customer journey was linear. The manufacturer produced products and delivered them to the customer, and the journey was at an end. Modern manufacturers have shifted the customer and the product to the center of the value chain, rethinking their business models and engineering smart products that go beyond just function to provide new services that deliver ongoing value to customers.
What’s the ultimate goal of having all of this data? Getting important insights that can help you drive your business forward. This not only means understanding what happened in the past or what is happening at this moment, but also predicting what will happen in the future. Things like predicting equipment failure, anticipating customer needs or foreseeing catastrophic events. Manufacturers are looking for tools and services that will enable them to turn field service from a cost center to a profit center. You can do this with Azure AI.
Concern
Eroding margins and rising costs
Dynamically changing customer needs & product variability
Growing skills gap & deteriorating assets
Solution
Increase operational efficiency, automatic asset maintenance, and less asset replacements
Predictive inventory management, customized quoting and contracting
Improve reporting, more natural interfaces, and efficient training
What does the ‘Factory of The Future’ look like?
Product-as-a-service isn’t just an industry buzzword: it’s imperative for staying competitive with a fanatical focus on customer outcomes.
Making this transition means enabling new business models and fundamentally rethinking the entire manufacturing value chain. Technology such as cloud & hybrid cloud computing, AI, IoT & Edge computing, High Performance Computing, mixed reality and digital twins, Blockchain and Quantum Computing can help you do just that.
Here are seven key digital transformation scenarios that can help you advance your journey to product-as-a-service.
Workforce Transformation
The modern workforce for manufacturing needs new skills to keep up with the digital transformation and speed of business that impacting every one of the scenarios we’ve talked about so far. Even without this transformation there’s already a skills gap in manufacturing. Workforce transformation requires that we se technology to attract, train, and retain the next generation workforce, equipping them with the skills to reimagine manufacturing, and shape our sustainable future. thyssenkrupp is one of many manufacturers putting the adoption of “employee empowerment” technologies at the center of their digital transformation.
Connected Product Innovation
You can use all this data coming in from IoT sensors, field service, sales, factories, and the supply chain to speed innovation. With connected product innovation solutions, you can get real-time insight into which products and features customers are using without waiting for customer survey results. And with big computing capacity available on demand, you can iterate the next version of your product much more rapidly using digital twins, as well as simulation and analysis tools. The Automotive industry is doing this on a massive scale with the data coming in from their connected vehicles, and fleets of specially instrumented autonomous vehicles. EFS is doing using this data to teach the next generation of vehicles how to see the real world. But any IoT connected machine provides this opportunity for a digital feedback loop. You can also get more accurate, timely data on which parts failed and what the best problem resolutions were so you can improve product and service performance. These are just a few ways you can analyze data to realize a faster speed-to-market and improve the quality of your products and services, or product-as-a-service!
Connected Field Service
An ideal first step in moving toward product-as-a-service is proactively engaging with your customer throughout your product’s lifecycle.
With connected field service solutions, you can remotely monitor the smart product you’ve sold to your customer. That way, you can get the insights you need to do predictive maintenance—and minimize your customer’s downtime.
For both predicted and unexpected maintenance issues, you can speed up repair time by getting alerts and dispatching technicians using skills-based assignments—and by empowering service technicians with complete customer insight, real-time guidance, and cross-team collaboration. Customers like Chevron are doing this in their refineries, ExxonMobil, in their Oil Field Services in the Permian Basin, thyssenkrupp with their elevators, Sandvik Coromant with their CNC machine tools, Rolls Royce with their aircraft engines, Ecolab with their water treatment and savings services, etc…
Connected Sales & Service
Delivering your product-as-a-service also means you need to take a new, collaborative approach to the sales process to help sellers navigate your increasingly complex portfolio of products and services, and to build long-term relationships and ongoing customer loyalty.
With connected sales and service solutions, you can empower your sellers to see the full spectrum of a customer’s needs. Sellers can analyze previous product usage and performance, and then predict potential needs using intelligent tools.
Sellers can also collaborate with customers to customize product purchases and efficiently execute contracts using configure-price-quote, quote-to-cash, and contract lifecycle management tools. These tools can shorten the buying cycle and help the customer get precisely what’s needed. And there’s the call center of the future, where you can tap into the insights gleaned from your smart connected products to improve the effectiveness of your customer service agents using virtual agents or bots, like HP is doing to handle the 600 million service inquires they get annually.
Factory of the Future
To customize your products and services for your customers—and innovate at the speed that product-as-a-service requires—you need an agile, responsive production process. You need solutions that can help you enable a “factory of the future.” To accomplish this, you’ll need a complex ecosystem of self-regulating machines and sites that customize output, optimally allocate resources and offer a seamless interface between the physical and virtual world.
The journey to factory of the future starts with connecting factory assets—adding sensors to machines and equipment to collect data, then monitoring and adjusting operations accordingly. Ultimately, you’ll want to connect and monitor factory performance across the globe, using data from smart assets to apply operational insights and further optimize your production processes. This is where even the most advanced manufacturing service providers such as Jabil, or the Industrial Automation giants such as Rockwell Automation, Schneider Automation, Siemens etc, are finding new opportunities by augmenting operational technologies (long powered by Windows embedded technologies), with new IT capabilities such as IoT, AI, Mixed Reality and secure and compliant communication and collaboration cloud capabilities.
Intelligent Supply Chain
As you’re making more product variants—and delivering customized connected services along with them—your supply chain becomes ever more complex and multifaceted. You can use intelligent supply chain solutions to help you manage that complexity. A new generation of intelligent business applications, can help you: 1) deliver the right products, parts, resources, and service where and when they’re needed, 2) achieve a balance between desired customer service level and budget requirements, and 3) enable tighter upstream and downstream collaboration across increasingly complex value chains. Caterpillar is able to reduced their parts inventory by 10-15% by leveraging O9 Solutions “born in the cloud” Integrated Business Planning solution
Sustainability
Sustainability matters. It matters to the modern workforce. It matters to your customers and to all of our stakeholders. Leaders in manufacturing, like Ecolab and Buhler Group are stepping up to help build a future by eliminating waste and engineering better outcomes for all their stakeholders, designing for sustainability throughout the end-to-end value chain and lifecycle of their products and services.
These solutions are built on a multi-step platform consisting of three distinct horizons:
Connected: Build digital foundation. Leverage the cloud to connect, automate, visualize end-to-end view of the business.
Predictive: Drive agility, responsiveness and flexibility by moving from reactive to predictive with IoT, high performance compute, and machine learning.
Cognitive: Develop disruptive capabilities to enable new business models amplified with algorithmic decision making and automated execution.
The vast majority of existing architectures that run the manufacturing environment today were made many years ago when cloud, large storage capabilities, fast computing environment, ease of visualization/interaction or the ability to aggregate data from unstructured environments were not possible. There’s a shift in how these systems can be enhanced today in a fast and inexpensive way. There’s also the ability to integrate a larger ecosystem with data flowing from any layer of the system from any location where the equipment exists. Therefore, what used to be limited to the four-walls [of the plants] within one organization is now securely and safely shared across many internal or external organizations allowing to reduce cost, improve efficiencies and accelerate competitiveness for the participants in the new ecosystem.
Get connected through a common communication model
Connecting machines on the plant floor is the first and most significant barrier to realizing a Factory of the Future strategy. Most existing manufacturing machines are not Internet-enabled and some even have propriatery operating systems which make it extremely difficult to access the data. Most manufacturers have heterogeneous manufacturing sites—maybe you’ve added state-of-the-art cloud-enabled machines as you’ve built new facilities but you still retain legacy equipment that lacks sensor capabilities. With Microsoft’s broad partner ecosystem enabling you to retrofit any legacy equipment with sensors, achieving end-to-end visibility with the machines you already have is easy. Connected factory enables you to connect individual pieces of equipment at your own pace, with no need to connect everything at once or disrupt production. Want to experiment by connecting one machine now, and the entire assembly line starting next week? You have the flexibility to do that. Want to connect everything quickly and start getting insights as soon as possible? Your old equipment won’t slow you down. Connecting your equipment empowers you to consolidate data across machines on the cloud, via edge gateway devices, enabling you to centralize while achieving powerful controls and protection.
Develop predictive dashboards to allow global visibility
With your machines connected to the cloud, you can empower your employees with near-real-time visibility into performance, whether they’re on the factory floor or at headquarters. Intuitive, visual dashboards ensure timely detection of anomalies, so your employees can order adjustments and repairs before operations are impacted. This drives improved utilization, reduced waste, targeted cost savings, and improved quality.
- Aggregate data from machines across your manufacturing sites to enable a holistic view of key performance indicators
- Drill into your data to compare the performance of equivalent machines at multiple sites
- Gain insight into the factors that contribute to variations in performance
Leverage cognitive capabilities to optimize operations
Once a manufacturer has migrated to the Cloud and employed machine learning to identify trends and patterns in the operational data, the next step is to leverage AI to enhance decision making and automate the manual, repetitive tasks that can be handled without human involvement. There’s a saying that machine learning is used to make predictions and AI is used to make decisions. Imagine capabilities that both accelerate throughput and increase accuracy by using AI to make decisions. Examples include using a high-speed camera with a ML model trained to detect microscopic quality issues in fractions of a second. Allowing the AI to determine if the quality issue should be scrapped or sent to rework will reduce variability on the line and capture quality issues before they reach a customer. While cognitive vision for AI may be a ‘lights out’ operation which requires no human involvement, Microsoft is positioning AI as a human-enabler to enhance decision making and asset productivity.
Crawl: Not surprisingly, the first step toward an intelligent factory is getting connected. You can connect factory sensors to Azure IoT Hub, which features automated, secure device provisioning, and then start feeding your applications new intelligence on equipment and processes. By ingesting, analyzing, and visualizing assembly line data in near real-time, you’ll have access to reporting at a glance (including performance, efficiency, and output data), factory level KPI’s, production line details, machine-specific analysis, targeted alerts for outages or anomalies, and more.
Walk: From there, the next phase is using something like Dynamics 365 to turn that information into action, such as calling a technician or triggering deeper, remote diagnostics with the click of a button. With a digital feedback loop up and running, you can start mining factory and business data for insights and patterns using advanced analytics and machine learning, which will help you optimize operations and leverage predictive maintenance effectively.
Run: Once you’ve enhanced a location or process with a digital feedback loop, the final phase is scaling that capability across your entire business. You can aggregate data across locations using Azure Synapse, which bridges data warehouses and data lakes for a global, unified view. And using Azure Synapse, your data professionals can prep and manage data from a single workspace while using native integration with Azure Machine Learning and Power BI to fuel new predictive models and streamline business intelligence and reporting as well.
Over the next several weeks, we’re going to take a deeper look into 5 key areas of manufacturing that are enabled by Microsoft Azure and other related Microsoft technologies.
If you should have any questions along the way, please feel free to drop us a note and we’ll have one of our Azure Engineers get in touch to talk about you own manufacturing initiatives.